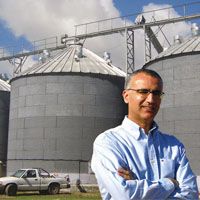
Uma unidade Armazenadora atualmente deve ser projetada para ter um sistema de qualidade contínuo em todas as suas etapas, ou seja, módulos de Recepção, Limpeza, Secagem, Armazenagem e Expedição. O equilíbrio de todas as etapas e suas compatibilidades de fluxo (t/h) proporciona uma qualidade final de produto armazenado, rentabiliza a safra do Produtor Rural e aumenta a renda no campo.
As unidades antigas tinham seus projetos desenvolvidos para receber, limpar, secar e armazenar, somente com o objetivo final de estocagem e comercialização sem agregar valor ao produto. Os projetos atuais de uma unidade armazenadora visam levar a um patamar de qualidade de armazenagem de forma a manter a “Identidade Preservada” dos grãos colhidos na lavoura, perpetuando sua origem e mantendo a “rastreabilidade” no processo de certificação de produto para comercialização aos grandes compradores internacionais e consumidores internos e exigentes.
Para atingir este estágio, necessitamos projetar as unidades observando alguns itens de extrema relevância técnica para adquirirmos o novo conceito “Garantia de Qualidade Armazenada”.
Na recepção, necessitamos ter inicialmente um sistema de eliminação ou captação de pó. O pó é o maior agente de contaminação numa unidade e sendo aspirado pelos seres humanos pode causar doenças mortais e alergias no corpo. Os projetos das moegas devem ser dimensionados para receber produtos de diversas características, segmentando conforme o perfil de colheita (produto sujo-úmido, sujo-seco, limpo-seco, seco-sujo e outras, variações como percentual de impurezas, umidade e variedades do próprio produto).
Desta forma, devemos projetar as moegas segmentadas (moegas duplas, moegas divididas, moegas duplas e divididas ou em forma de bateria). Estas opções de recebimento viabilizam a segmentação de recebimento. Com este processo bem realizado, as demais atividades terão seu rendimento melhor, pois trabalharão com produtos homogêneos.
O fluxo (t/h) de ligação entre os módulos é realizado por transportadores e canalizações (elevadores de caçamba, transportadores de corrente e helicoidais, correias transportadoras, chupins e outros tipos) e devem ter uma compatibilidade de fluxo e um dimensionamento de capacidade de 30% acima dos módulos (ex: módulo com 100 t/h – capacidade recomendada de 130 t/h), evitando os estrangulamentos de fluxo entre eles.
Para canalização, respeitar sempre a inclinação mínima, para termos um escoamento dentro do fluxo necessário. Para sementes a inclinação deverá ser menor que o padrão em relação ao grão comercial. Para redução de custos, quando trabalhamos com grãos limpos e secos (pós secador) poderemos ter uma inclinação menor que a tradicional, reduzindo altura de elevadores e custos de energia elétrica (quanto menor altura do elevador, menor a potencia necessária - CV).
Este sistema de interligação dever ser muito bem dimensionado e utilizado os dispositivos recomendados para minimizar os danos físicos nos grãos (uso de amortecedores de linha, para grandes distâncias de tubulação em queda vertical), e amortecedores na entrada das máquinas, direcionando de forma correta o produto no interior da máquina, evitando caminhos preferenciais e desgastes.
No módulo de limpeza houve uma grande mudança de conceito, pois hoje projetamos um “Sistema de Limpeza” analisando o grau de impurezas e umidade da massa de grãos que será processada, itens fundamentais para o dimensionamento do sistema. Quanto maior for o grau de impureza, menor será a capacidade, pois a máquina deverá ter mais tempo disponível para realização da limpeza. Para realizar este processo, regulamos a entrada de produto nas peneiras, através dos registros.
O mesmo ocorre para a umidade, quando maior for a umidade dos grãos mais lento será seu escoamento sobre as peneiras, acarretando necessidade de redução do fluxo de entrada. Exemplificando: uma máquina de limpeza de 100 t/h, para processar grãos com 18% de umidade e 4% de impureza, caso receba um produto com 6% de impurezas e 20% de umidade terá uma redução de 18% e 10% respectivamente, tendo uma redução acumulativa de 26,2% com a capacidade final ficando em 73,8 t/h.
Analisando no conceito de sistema no momento de projetar, iremos colocar uma com capacidade de 150 t/h ou duas de 80t/h=160 t/h (ver modelos de capacidades existentes no mercado) primando pela qualidade de limpeza e manutenção do fluxo. Dentro deste módulo possuímos a Casa de Máquinas e Moegas.
Estes locais devem ser dimensionados para possibilitar uma boa movimentação para operação e possuir um sistema de captação de pó, tanto na moega como na limpeza, como também, sistema de exaustão, observando ambiente amplo com circulação de ar, para evitar o acúmulo de gases e concentração de pó. Quando maior for a circulação de ar, maior será a qualidade de trabalho e menor contaminação e poluição atmosférica.
Na secagem (módulo), devemos observar os mesmos aspectos da limpeza, incluindo as condições climáticas da região. Secar soja numa região com umidade relativa alta e temperaturas baixas é diferente que secar no Centro Oeste, com umidade relativa baixa e temperaturas altas. Neste último, o rendimento do secador é melhor e, consequentemente, a capacidade de secagem aumenta (t/h) e o consumo de energia diminui (lenha).
Considerando estes aspectos, dimensiona-se qual o secador mais adequado para sua região, lembrando sempre que os secadores devem ter uma capacidade mínima de 30% acima da especificação nominal, para atender estas variáveis e agilizar o processo de descarga na primeira carga e em caso de secagem intermitente.
Todos os processos em uma unidade convergem para a armazenagem e conservação dos grãos. Podemos até afirmar que todos os investimentos e aplicações feitos durante o ciclo de produção, iniciando pelo preparo da terra, plantio, aplicação de defensivos e compra de máquinas, convergem para a estocagem. Momento de maior importância no processo, onde o produtor pode manter seus investimentos e rentabilizar o negócio, ou perder todo o trabalho realizado anteriormente. Este é o momento da verdade, um projeto destinado à qualidade de armazenagem, terá seu desenvolvimento para diminuir ao máximo as perdas qualitativas e quantitativas.
Armazenagem
A Armazenagem de Grãos está alicerçada em três grandes pilares, com a premissa de já termos executado a secagem e limpeza de acordo com os padrões atuais de qualidade de processamento e das especificações (instruções) do fabricante: 1- Monitoramento da massa de grãos; 2- Aeração; 3 - Sistema de Exaustão, também chamada hoje de Aeração Natural ou Intensificada.
Para o monitoramento, possuímos sistemas de gerenciamento que coletam dados através de sensores instalados no interior da massa de grãos, que são monitorados por software, proporcionando ao armazenador uma relação de dados para tomadas de decisões rápidas e assertivas. Aeração, também tem sua importância, deve ser dimensionada para as condições de armazenamento conforme perfil da região, não desconsiderando o histórico climático.
Sistema de Exaustão:
Sobre os itens mencionados acima temos o “Sistema Cycloar de Exaustão” que é um novo conceito na armazenagem, fundamental para termos uma qualidade. Esta aeração natural ou intensificada proporciona equalização do ar entre a massa de grãos e a cobertura do telhado, diminuindo o calor proveniente da radiação solar e eliminando o “bolsão de ar quente” (massa de ar quente e saturada), bem como a condensação sob o telhado, nas chapas laterais dos silos e paredes dos armazéns e o consequente gotejamento sobre os grãos.
Este sistema proporciona outros benefícios relevantes como uniformidade na massa de grãos, aeração permanente e contínua (extrai calor do ambiente, pó, gases, umidade do ar), evita o apodrecimento (deterioração, mofo, germinação), inibe a proliferação de pragas e, aliado a tudo isso, preserva a estrutura física do ambiente, pois evitando a condensação, elimina itens como o surgimento de pontos de corrosão na estrutura metálica do telhado, o umedecimento das correias (borracha) dos transportadores dos armazéns com carga realizada por Correia Transportadora (Cinta Transportadora) e o sobre-aquecimento nos acionamentos aumentando a vida útil dos mesmos e suas transmissões.
O gotejamento em silos e armazéns, ou seja, a condensação, é um fenômeno físico e grande inimigo da armazenagem. A taxa de umidade varia conforme a temperatura significando que, quando o ar quente aumenta sua capacidade de absorver umidade, diminui quando o ar esfria. A radiação solar provoca o aquecimento da cobertura (telhado) e, pela condução térmica, aquece o ar interno, baixando a umidade relativa do ar. Esse ar com a temperatura elevada absorve a umidade contida nos grãos armazenados pelo efeito da evaporação.
Em contra partida, quando este ar úmido entra em contato com a cobertura resfriada, pela variação de temperatura externa, cai a temperatura do mesmo elevando a umidade relativa interna, podendo com isso ultrapassar o ponto de saturação, condensar e gotejar sobre o produto armazenado, gerando o mofo, a deterioração e até a germinação dos grãos na camada superior da massa. Em alguns casos acontece o gotejamento e no dia seguinte, com a irradiação da chapa decorrente do sol, seca a camada superior, mas como os grãos são um isolante térmico, as camadas úmidas mais profundas, acabam apresentando mofo e demais conseqüências já mencionadas.
Ou seja, uma camada incrustada e invisível para quem observa a massa numa visão superior, por cima grãos de forma bonita (sadios), mas a baixo, grãos podres. Esta camada deteriorada cria uma grande barreira para a passagem do fluxo de ar quando se realiza a aeração.
Dependendo da espessura e dos graus de deterioração desta faixa, chegamos a uma perda de eficiência de até 60% (medido “in loco”), reduzindo a vazão de ar que atravessa a massa de grãos, comprometendo a aeração e aumentando as perdas técnicas (qualitativas e quantitativas).
Dentro deste novo conceito e descrição acima, consideramos o “Sistema Cycloar de Exaustão” como fundamental para toda a conservação. A não utilização gerará perda em todos os investimentos anteriores.
As unidades atuais devem ser projetadas com critérios que proporcionam segurança de operação, qualidade garantida, compatibilidade de fluxo em relação aos módulos e recebimento da produção (safra).
Os poços de elevadores e moegas devem ser projetados de forma que sua profundidade não ultrapasse o nível do lençol freático, evitando infiltração de água. Construir túneis e caneletas com dimensões que possibilitem acesso de forma direta e fácil para ocasiões de extrema urgência (acidente) é importante e aqueles que estão localizados sob baterias de silos, armazéns e moegas, devem ter sistemas de circulação de ar e possibilitar a passagem de pessoas, quando necessário.
Todos os poços e túneis devem ser projetados para evitar o depósito de gases oriundos do processo respiratório do grão e deterioração do mesmo. Instalações elétricas devem ser aparentes e superiores, com proteção contra roedores e outros.
As unidades armazenadoras devem focar a sua concepção num projeto que garanta a qualidade final do produto armazenado, segurança, valorização dos benefícios e ferramentas que hoje estão disponíveis aos armazenadores, como Automação, Sistemas de Exaustão e Controle a Distância da massa de grãos e, aliado a tudo, a capacitação dos operadores.
Estar preparada para futuras ampliações e localizada em ponto de fácil logística na propriedade é importante e estratégico para o crescimento, tendo sempre como princípio o fato de ser um local limpo, de fácil circulação e operação. Estes são alguns de muitos detalhes que devemos observar quando da elaboração de um projeto e construção de Instalações de Armazenagem.
Projetar Segurança
Projetar para segurança operacional é o principal foco dos armazenadores e nossa responsabilidade é relacionar detalhes para aplicar na obra:
a) Projetar a instalação armazenadora, destinando locais para depósito de materiais como ferramentas, lenha, peças de reposição, sucatas, combustíveis, embalagens de produtos, etc;
b) Identificação dos equipamentos a nível visual do operador, instalação de placas identificando setores da Unidade (recepção, almoxarifado, laboratório, etc.);
b) Identificação dos equipamentos a nível visual do operador, instalação de placas identificando setores da Unidade (recepção, almoxarifado, laboratório, etc.);
c) Pintura de segurança nos pontos de perigo (amarelo/ laranja).
Utilização de EPIs (máscaras para proteção contra pó, luvas, botas de segurança, capacetes, óculos de segurança, trava-quedras);
Utilização de EPIs (máscaras para proteção contra pó, luvas, botas de segurança, capacetes, óculos de segurança, trava-quedras);
d) Projetar fechamento (importante a possibilidade de passagem de ar) nas bordas dos poços com porta de inspeção para evitar quedas de pessoas;
e) Guarda corpo nos elevadores, passarelas e demais locais necessários;
f) Proteção nos acionamentos (polias e correias);
g) Luminárias a prova de explosão;
h) Sistema de renovação de ar em poços e túneis, para retirada de gases acumulados;
i) Projeto de sistema de combate a incêndios;
j) Projeto sistema de proteção contra fenômenos naturais;
l) Visitantes devem sempre ser acompanhados por profissional da unidade;
n) Identificar os operadores nas atividades noturnas na unidade, sempre com duas pessoa ou mais;
m) Utilização de equipamentos de proteção coletiva EPCs (lanternas apropriadas, detector de gases, sistema de captação de pó, aparelhos de comunicação (radio), sistema de renovação de ar/exaustão).
Importante é termos o conhecimento da necessidade de uma higienização, um plano de manutenção preventiva e corretiva e de um programa de capacitação dos operadores que atuam nas áreas operacionais, o programa deve possibilitar treinamento e reciclagem. Isto contribui para a qualidade e a rentabilidade da safra armazenada.
Uma equipe capacitada para operação, com o domínio das melhores práticas, complementa e garante uma safra rentável.