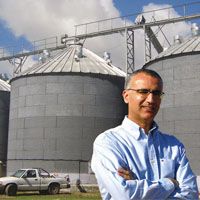
Para reduzir a umidade dos grãos é necessário que um volume de ar com umidade relativa (U.R) baixa cruze pelos mesmos e durante o tempo de contato absorva a água sem ultrapassar o limite de pressão interna do grão, mantendo intacto o tegumento (casca), proteção natural contra insetos, pragas e outros.
Os secadores contínuos estão dimensionados para realizarem essa operação num regime de 24 horas e é fundamental para o funcionamento, o equilíbrio do ar entre a vazão (volume) e sua condição térmica (Temperatura / Unidade Relativa) para termos um rendimento pleno.
Ao iniciar o funcionamento do secador contínuo devemos observar itens como: os ventiladores estão desobstruídos, girando livremente e para o sentido correto; o interior está limpo sem impurezas e grãos nos dutos e piso; os termômetros e controle de nível estão funcionando corretamente; os registros de ar de resfriamento e reaproveitamento estão na posição correta e bem fixados; o sistema de descarga esta lubrificado/ limpo; inspecionar e regular a descarga conforme o tipo (eclusas, bandeja, pneumática).
Lembramos, por segurança, nunca entrar no funil de descarga com o transportador de descarga ligado e com os ventiladores em funcionamento. Quando em manutenção, desligar a chave geral do equipamento e identificar de forma clara os motivos pelos quais está fora de operação.
A secagem contínua é o processo onde os grãos entram úmidos (18% b.u ou acima) e saem frios (de 5º a 10°C acima da temperatura ambiente) em condições de serem armazenados adequadamente nos parâmetros de umidade desejados e de segurança para uma boa conservação.
A tarefa de iniciar o processo tem como primeira ação acender o fogo durante a carga do secador para agilizar o processo. Na fornalha, manter as portas dos cinzeiros abertas, as portas de alimentação do combustível fechadas e as venezianas de mistura de ar do secador abertas.
Posicionar o fluxo do sistema de modo que o produto que esteja saindo do secador (primeira carga) ainda úmido retorne ao secador, acionar o elevador e quando o produto atingir metade da torre da secagem, acionar por alguns minutos a descarga, com o objetivo de evitar vazios na torre, deixando a massa de grãos distribuída uniformemente no interior.
Concluída a carga, ligar os ventiladores iniciando a secagem dentro do processo intermitente, ou seja, fazer o produto que sai do secador, retornar ao mesmo, com o operador observando e colhendo amostras (período entre 15 a 30 minutos) para saber quando o primeiro produto que saiu do secador já deu uma volta completa e chegou a umidade determinada. Nesse instante iniciamos a secagem contínua.
Na sequência, iniciamos a carga do secador com produto pré-limpo, pois as impurezas em excesso além de diminuir o rendimento do secador, influenciam no fluxo interno dos grãos e podem gerar incêndio na torre, lembrando que o incêndio sempre é decorrência do acúmulo de impurezas.
O processo de descarga de produto seco e carga de produto úmido podem ser repetidos no máximo 3 vezes, quando, então, o secador deverá ser inspecionado e limpo.
As impurezas, uma das causas mais comuns e o excesso delas dentro do secador, que por não se deslocarem com a mesma velocidade dos grãos vão se sobre-aquecendo até que entram em combustão gerando foco de incêndio.
A solução para este problema é a limpeza periódica de toda a torre de secagem removendo palhas e outras impurezas que tenham se acumulado.
Caso ocorra um incêndio, proceder da seguinte forma: o operador deverá fechar todas as entradas de ar do secador, pois sem oxigênio não haverá combustão, imediatamente desligar os ventiladores, parar de alimentar a fornalha, fechar todos os registros de ar do secador e fornalha, desligar os equipamentos e os demais que estão no fluxo.
Após a queima concluída, descarregar e limpar o local do sinistro. Em situações extremas onde o fogo se alastrou pela torre, acelerar a descarga, depositando o material em um local próximo, não permitindo que seja transportado por outros transportadores pelo fato de os grãos aquecidos (queimados) danificarem correias, caçambas plásticas e demais componentes.
Nota: Jamais utilize água para apagar o incêndio.
Em caso de falta de energia elétrica durante a operação, abrir todas as venezianas de todas as aberturas, evitando o aquecimento.
Retornando a energia, proceder de forma contrária. Caso o produto esteja com um grau de umidade elevado e a parada for longa, recomenda-se remover o produto para a recepção (moega) evitando a formação de gases na torre decorrentes do processo respiratório do grão, e, consequentemente o risco de explosão.
O ponto de maior importância na operação do secador é o monitoramento contínuo das pressões internas do secador e da temperatura de secagem.
As pressões são medidas através do aparelho chamado de Psicômetro, e deve ser instalado no corpo e nos pontos indicados pelo fabricante, pois cada um tem suas pressões de trabalho definidas, e que devem ser respeitadas quando da operação.
Considerando que o ponto mais crítico e importante está entre a torre de secagem e os ventiladores, podemos exemplificar a situação: neste ponto a pressão de trabalho média deve ser 27 mmCA (conforme fabricante).
Caso estejamos trabalhando acima, nosso secador está com falta de ar (venezianas fechadas). Caso esteja abaixo deste patamar, estamos com muito ar ou com a torre de secagem incompleta e ambas as situações comprometem a capacidade de secagem.
Trabalhar com as pressões internas do secador equilibradas conforme especificação do fabricante e a temperatura de trabalho contínua são itens fundamentais para atingir as capacidades especificadas (t/h).
A operação acima está sendo gradativamente substituída por sistemas de automação, com aparelhos que indicam as condições de todo o processo de secagem, apresentam um rápido sistema de coleta de dados que são realizados em segundos, indicam e controlam as temperaturas de secagem e da massa de grãos na entrada e saída, umidade de entrada e saída, nível mínimo e máximo do secador, possuem alarmes de temperatura, umidade e nível de carga e controlam o sistema de descarga variando sua velocidade conforme as condições de operação e secagem.
Todas estas informações são armazenadas em um banco de dados e possibilitam a impressão e visualização em gráficos no monitor, contribuindo para tomadas de decisões imediatas, possibilitando, inclusive, realizar este monitoramento e alterações ou correções dos parâmetros à distância, através da Internet.
Este processo contribui para realizar uma operação eficaz, com uma qualidade de secagem superior e com rendimento de produtividade maior, aliando economia de combustível.
Quanto à operação da fornalha, esta deve ter uma alimentação contínua de lenha na câmara de combustão, com distribuição uniforme sobre as grelhas, fazendo com que o ar cruze por toda a lenha, e não somente pelos vazios.
Se o operador fechar todas as aberturas da fornalha com o objetivo de diminuir o consumo de lenha, terá como resultado uma combustão incompleta e a redução da vazão de ar de secagem, podendo ocorrer uma pressurização do sistema causando arraste da fagulhas que ao encontrar grãos mais aquecidos ou palhas já sobre aquecidas pode fazê-los entrar em combustão.
Uma secagem correta permite uma qualidade de armazenagem e segurança do produto, possibilitando conservar por um tempo indeterminado, até a melhor oportunidade de comercializá-lo.
Ter operadores capacitados para estas operações em uma unidade armazenadora é fundamental e necessária para o Brasil atingir a liderança no cenário do “Agronegócio Mundial”.