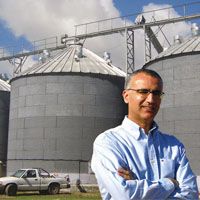
A busca contínua pela redução das perdas quantitativas e qualitativas no processo de armazenagem é de fundamental importância para a conquista de uma liderança mundial no que se refere à produção e estocagem de grãos. A busca por essa proposta e desafio levou o Brasil a desenvolver equipamentos avançados de gerenciamento (Sistemas Controladores Automatizados) de forma gradativa e isolada em relação às demais etapas da cadeia agrícola do produtor, acompanhando a evolução da Informática e Engenharia Eletrônica.
Os avanços e a possibilidade de unificá-las entre si, possibilitaram termos uma a Armazenagem com mais Precisão em todas as etapas do processo de beneficiamento - recepção, limpeza, secagem, armazenagem/ conservação de grãos e gestão administrativa/ operacional.
Existem sistemas para secagem e monitoramento da massa de grãos armazenada em silos verticais ou armazéns que têm como objetivos reduzir erros de processo e desvios de operação, registrando e formando um banco de dados para tomada de decisão imediata e correção do processo instantaneamente.
Na secagem, o objetivo da atividade é processar com uma temperatura contínua e dentro dos parâmetros definidos pelo fabricante, reduzindo a danificação dos grãos (queima, fissuras no tegumento, etc.) e manter a capacidade nominal dentro de um fluxo (t/h) que proporcione rendimento máximo do secador com equilíbrio termo-dinâmico.
Os sistemas evitam problemas de falta de alimentação de combustível (lenha, casca de arroz, óleo, ou outros) na fornalha (fonte geradora de calor), risco de incêndio, danificação dos grãos por estarem expostos a altas temperaturas e promovem um equilíbrio entre vazão de ar (quente e frio). Controlar as pressões internas e as temperaturas na torre de secagem, são itens que buscamos continuamente, melhorando o rendimento de secagem (fluxo) e proporcionando economia de combustível com qualidade final.
Os sistemas atuais indicam e controlam a temperatura (°C) em até quatro ou mais sensores instalados e distribuídos dentro do secador, indicando umidade de entrada e saída do grão, monitorando o nível mínimo e máximo da coluna de secagem com alarmes de temperatura, umidade e nível interno, comandam e controlam todos os tipos de descarga - pneumática, mecânica-temporizada ou com inversores de frequência - variando a velocidade no painel de comando.
São operações que anteriormente eram realizadas de forma manual e registradas em planilhas avulsas, não possibilitando o cruzamento de informações e muitas vezes sendo perdidas nas salas de comando. Estes dispositivos de medição podem ser instalados em qualquer secador, atual ou antigo.
De fácil adaptação, são colocados sensores (temperatura, umidade, pressão e outros) e equipamentos de regulagem de entrada de ar no secador, todos gerenciados por um software.
Os sistemas de precisão permitem o acesso e acompanhamento do processo de secagem e outros de qualquer lugar, via Internet, com dados visualizados no equipamento pelo software, em tempo real. Toda a informação armazenada é compilada em forma de gráficos e planilhas.
Os sistemas inteligentes de gerenciamento da armazenagem abrangem termometria, aeração e controle de estoque. São equipamentos que controlam com máxima eficiência a qualidade os grãos armazenados e possibilitam ao operador inúmeros recursos para realizar um trabalho de precisão. Com isso, acontece um gerenciamento completo da unidade, acompanhando a aeração, volume de estoque, temperaturas máxima e mínima e as médias internas dos grãos.
Os focos de calor são detectados por sensores (cabos de termometria) e visualizados através do recurso de imagem térmica de forma dinâmica, podendo fixar pontos com valores e realizar comparações da variação de temperatura durante um período.
O gerente da unidade tem a possibilidade de programar o envio automático de relatórios de temperatura e alarmes de focos de calor e outros dados para endereços de e-mails e celulares, acompanhando 24 horas por dia o comportamento da massa de grãos e a eficácia da operação de forma total.
Como segurança, também existe a opção de observar o nível do talude dos grãos em cada silo ou armazém e obter informações sobre carga ou descarga dos grãos com a possibilidade de valorizar (R$) o que possui estocado e o que está sendo expedido com precisão.
Na aeração, definimos os padrões de trabalho que desejamos para cada cultura - soja, milho, arroz, trigo, cevada, aveia, etc. - quanto aos limites de temperatura e umidade dos grãos armazenados. De forma programada, este sistema é acoplado a uma estação meteorológica que realiza leituras instantâneas das condições climáticas vigentes. Assim, a previsão de termos desvios de calibragem e leitura é mínima.
Nas condições determinadas pelo operador, os ventiladores (exaustores) são acionados para realizar aeração de resfriamento, correção, seca-aeração ou manutenção. Assim conseguimos registrar todos os dados disponíveis para análise e verificar também o consumo de energia, possibilitando fazer a conta do custo e do beneficio da armazenagem.
Hoje o processo de armazenamento de grãos está simplificado na medida em que dominamos as ferramentas automatizadas que o mercado disponibiliza para nós. Ficamos com históricos de operação acima de 10 anos, o que contribui muito para desenvolver e perceber como são as variações e as características na região que está instalada a unidade armazenadora.
Armazenar no sul do Brasil é muito diferente de armazenar no Centro Oeste, onde as temperaturas são mais elevadas e a umidade relativa (U.R.) são, em média, mais baixas. Estes registros nos possibilitam criar metas de ação de redução das perdas técnicas (quantitativas), ou seja, só podemos determinar metas quanto possuímos uma sequência de históricos e suas variações.
No processo de limpeza, para melhorar a qualidade final do produto, existem equipamentos que regulam a rotação do exaustor, aumentando ou diminuindo a velocidade do ar dentro do corpo da ventilação (câmara gravitacional), evitando arraste de produto para o ciclone ou excesso de impureza na massa de grãos.
Em caso de excesso de impurezas o sistema bloqueia a alimentação numa ação em cascata, da maquina até a moega (ponto inicial da alimentação). Para a variação de tamanho dos grãos, os sistemas operam na inclinação das peneiras aumentando ou diminuindo a capacidade de processamento.
No ciclone, temos controle de nível máximo para quando estiver no limite das impurezas e, também, sensores de pressão interna do mesmo, facilitando a regulagem da abertura do ar que atravessa a massa de grãos arrastando as impurezas leves, quando da entrada na máquina.
Todos os sistemas que compõem este conjunto de precisão possibilitam a verificação das horas trabalhadas de cada motor (equipamento) e tempo de parada para manutenção. Com estes dados podemos calcular o desgaste das peças e atuar ou programar uma manutenção preventiva, tendo as peças críticas em estoque para agilizar o ritmo de trabalho quando das paradas necessárias.
Na armazenagem de precisão também incluímos os sistemas de gestão que geram todos os processos administrativos de uma unidade armazenadora, como romaneios, notas fiscais, contratos, serviços, contábil, financeiro, fiscal, produção, suprimentos, atendimento a clientes e custos de manutenção - preventiva e/ ou corretiva.
São ferramentas que geram todos os tipos de controles, desde o recebimento até a expedição e comercialização do produto, incluindo custo de produção e margem de lucratividade atual e futura, com previsões de valores e controles rigorosos de dados e informações precisas para tomada de decisão. Inclui, também, a gestão de contratos com controles integrados de saldos de produtos, classificação, quebra técnica e prestação de serviços (secagem e armazenagem).
Ao conjunto dos sistemas de operação de limpeza, secagem e armazenagem, com a gestão dos processos administrativos/operacionais, conceituamos como “Armazenagem de Precisão”, que possibilita ao produtor aumentar sua rentabilidade, reduzir as perdas (quantitativas e qualitativas), que na armazenagem chegam até 7,5% dependendo da cultura.
É fato que o mercado onde o Brasil está inserido apresenta ferramentas para sermos competitivos o que, aliado à capacitação dos profissionais que operam estes processos, permite dimensionar a extrema importância e saber quais a conseqüências e os custos de uma armazenagem inadequada e mal operacionalizada.
O Brasil é a ultima fronteira agrícola do mundo. Necessitamos avançar de forma profissional, rentabilizando o campo e reduzindo as perdas, pois estas, caso ocorram, teem seu custo dobrado.
O processo de transferência de um sistema manual para um automatizado de forma completa, como acima descrito, pode ser executado em etapas, minimizando o investimento inicial. A cada etapa implantada, somente com o ganho de operação e produtividade, já acontecerá enorme contribuição não somente para pagar o investimento já realizado, mas também o próximo e, assim, sucessivamente até o final de toda a implantação.
A partir desse momento, os ganhos financeiros serão destinados a novos investimentos tanto em máquinas e implementos agrícolas como também em armazenagem e infra-estrutura no campo.
A visão de empreendedor mostra que necessitamos avançar tecnologicamente e sermos treinados, para sermos competitivos mundialmente.